Drilling
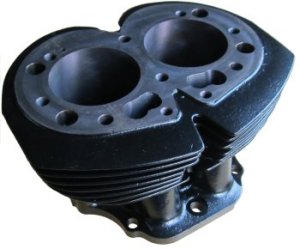
It is readily apparent, when giving anything more than a casual glance at a motorcycle, that even this two-wheeled form of transportation is made up of a considerable number of individual parts, each needing to be fixed in place by means of screws, bolts, studs or other similar fasteners, in order to perform their designed function.
It is therefore not surprising that each of these components requires holes of one type or another, for the fasteners to use, as well as others reasons, such as internal oil passages in engine components.
With such an amount of drilling necessary, these operations were carried out in more than one department at the AMC factory, usually on the basis of the material being machined (steel, cast iron or aluminium) and also on the size of the component.
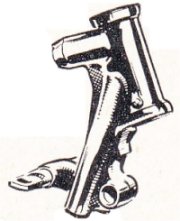
The ground floor Drilling Shop, next to the works entrance (later to be moved to make way for the Testers), was mainly concerned with the heavier work, especially that boring out of the malleable iron lugs that formed the tube joints of the old style Matchless and AJS frames.
This work required very rugged drilling machines to power the large diameter drills and equally rugged box jigs to accurately hold the workpieces during the process, prior to which tooling holes would have been drilled and reamed for locating purposes.
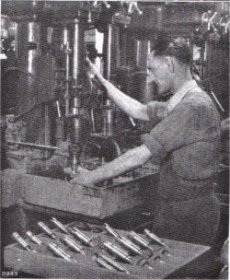
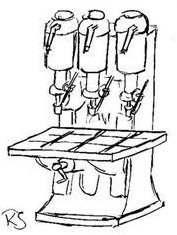
Other work would have entailed drilling, reaming, counterboring, tapping and spotfacing to be carried out in a sequence of operations on the same machine.
This was accomplished by using slip bushes and special quick-release chucks that allowed the operators to change the tools without having to stop the drill spindle.
Even thread tapping operations were carried out without interruption, by means of auto-reversing tap heads, although a delicate touch was needed by the operator in balancing the return spring pressure on the handle of the machine or otherwise risk breaking the tap.
The largest piece of equipment in the shop was a twin-spindled borer, used to machine the cylinder barrels.
It had a large rotating bed with three positions, one for the "rough cut" spindle, one for the "fine cut" spindle and the third, nearest the operator, the change-over position.
This set up thus allowed two cylinder barrels to be bored simultaneously, while the operator removed one finish bored workpiece and replaced it with a new raw casting.
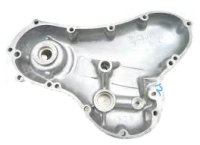
The second floor drilling shop was used mainly for the lightweight component machining and, for parts such as timing covers (shown), the machinery involved would have been fitted with multi-drill top columns to enable several joint face screw holes to be drilled simultaneously.
.jpg)
.jpg)
Other work, needing specialised tooling, would have involved the machining of hemispherical combustion chambers and valve guide/seat pockets in cylinder heads and was carried out in the third floor drilling bay.
As in most of the factory's production departments, the majority of operators in the drilling shops would have been relatively unskilled people and would be working a piece-rate system, with a bonus if they managed to exceed the production rate expected.
"Playing" the piece-rate system was a major pre-occupation with the operators, in order to obtain double, treble and even quadruple time bonus.
The game would involve the operator going as slowly as possible when the job was first being timed, taking deliberate care to use all of the safety guards provided and religiously cleaning the swarf away, before picking up the next part to be machined.
However, once the timing was recorded, the guards would be dispensed with and every effort was made to machine as many parts in the minimum time possible.
More experienced men, known as setters, would be responsible for the initial equipping of each machine with jigs, tools and gauges and checking that the job could be carried out to the accuracy needed in the required time, before allowing the operator to start work on a batch of parts.
The setter would also be required to intervene in the event of tool breakages or if the tolerances were no longer able to be held for any reason.
.jpg)
.jpg)
John Rourke spent over 30-years of his working life at AMC, some of it in the drilling bays.
You can read about his time there on Pages 14-15 of
'Memories of Plumstead'.
In 1962, the Dutch Motor magazine published a series of articles following a tour of the Plumstead Road factory.
You can read their extensive observation of the Drilling department in Parts 1 to 3 of
'This is How Your AJS and Matchless is made'.
(Note: The majority of the information was, however, previously published in the Alfred Herbert
'Machine Tool Review' article, a fuller version that can be found on the Links page).
Paddy Bodfish | ||
Ernie Davie | Setter | |
Frank Dent | Assistant manager | |
Bernard Fuller | 1956 - ? | brake linings |
Vic Lock | Setter | |
Charlie Ludbrook | 2nd I/C | |
Stan Perkins | Setter | |
Sammy Quilter | Foreman | |
John Rourke | (1928 - 61) | (dates incl. time in Grinding, Heat Treatment, Inspection and other departments) |
Reg Smith | Manager |