Capstan Lathes
.jpg)
In order to produce the vast number of turned components used in their range of motorcycles (engine/gearbox shafts and gears, wheel hubs, spindles and sprockets, steering and fork tubes, etc.), the AMC factory needed a very large turning department which, during their peak-production period of the mid-'50s, was re-housed in an extension of the original works, occupying the whole of the first floor and half of the second floor, and equipped with over 150 lathes of different sizes and types.
The department was known as the Capstans and/or the Herberts; the former name referring to the specialist type of lathe used for repetitive production work and the latter being the make of the machines.
The capstan type of lathe had evolved from earlier types with the addition of a an indexible toolholder that allowed multiple machining operations to be performed on a part, using a different tool in easy, rapid succession, with no need for the operator to perform setup tasks in between.
As the photograph below shows, the larger machines had turrets fitted with head steadies which engaged in turn with a large bar on the lathe body, to ensure that the machining forces did not affect the accuracy of the cutting tools.
.jpg)
.jpg)
Up to six different tools could be set up on one "turret" to allow drilling, reaming, boring, facing, countersinking and tapping operations to be carried out, all with their own depth stops and feed rates pre-set up.
.jpg)
To carry out a particular sequence of machining operations, the first tool would be positioned in-line with the chuck and fed forwards to carry out its cutting role. On retraction, the turret would then index around to bring the second tool into play and this would likewise be fed towards the work part, up to its own depth stop.
This sequence would be repeated until all the tools had been utilised and the finished part then removed from the machine.
For manufacturing long, cylindrical parts like gearbox shafts, the raw material would be in the form of standard sized bar (of either circular or hexagon profile) which would be fed through the rear of a matching collet chuck.
Components such as crankcases or fork sliders would have required special fixtures to hold the rotating castings, which would need to be carefully balanced to avoid generating dangerous vibrations when being turned at high speeds.
.jpg)
John Rourke spent over 30-years of his working life at AMC, some of it in the capstan bay.
You can read about his time there on Page 16 of
'Memories of Plumstead'.
In 1962, the Dutch Motor magazine published a series of articles following a tour of the Plumstead Road factory.
You can read their extensive observation of the Capstan department in Parts 1 to 3 of
'This is How Your AJS and Matchless is made'.
(Note: The majority of the information was, however, previously published in the Alfred Herbert
'Machine Tool Review' article, a fuller version that can be found on the Links page).
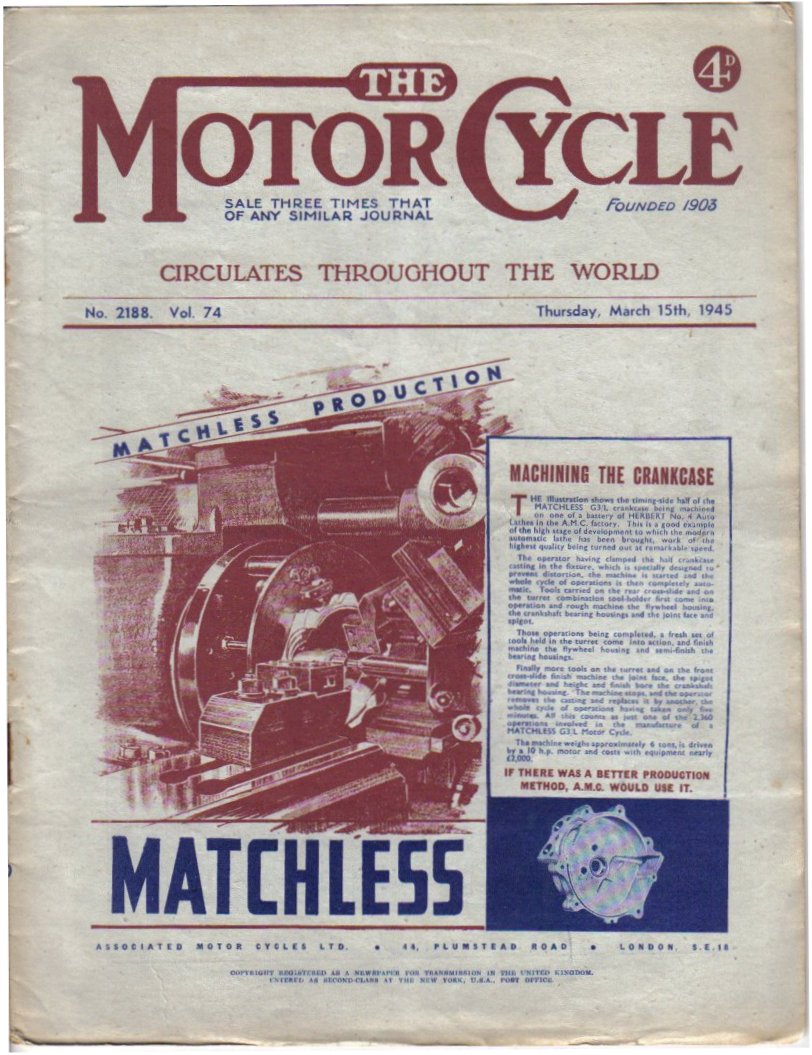
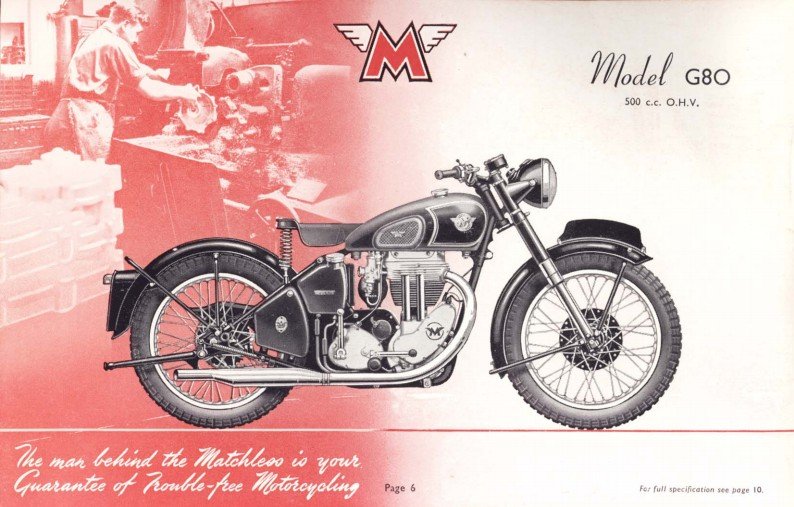
This Motor Cycle magazine cover page and sales brochure featured work carried out in the capstan lathe department.
(Click on the images to see enlarged views)
You can view the complete collection on Cover Pages.
Les Arnold | ||
(Mrs) Arnold | ||
Ken Blackman | ||
Colin Blackman | ||
Arthur Brooker | Manager | |
Charlie Cilia | ||
Frank Colwell | Setter | |
John Coshell | ||
Fred Dabbs | Chargehand | |
Alf Denman | ? - 1969 | Setter |
Morgan (Mogs) Drewell | ||
John (Jack) Garrett | ||
Jack Grimsey | ||
John Halsey | ||
Ron Maddocks | Machinist | |
Peter Stevens | Machinist | |
Tom Truelove | ||
Reginald Conie | Foreman |