Gear Cutting
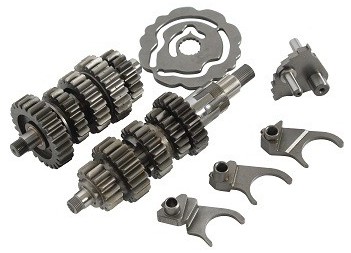
Gears, splined shafts and chain sprockets are important parts of a motorcycle and gearcutting forms an integral part of their manufacture.
Depending on the shape of the components, different cutting processes are used: Large diameter but thin parts, like a rear wheel chain sprocket, lend themselves to the gear SHAPING method whilst small diameter, long items such as splined gearbox shafts would use the gear HOBBING process.
.jpg)
In the hobbing process, a rotating, spiral-toothed cutting hob is slowly traversed along the length of the
component to be cut, with the relative drive to each part linked so that each full revolution of the hob
results in a one-tooth increment of the workpiece.
If a straight-cut gear is required, then the axis of the hob has to be tilted to match the lead angle of the hob's
spiral teeth, whereas a helical gear would need the hob to be angled to a correspondingly greater extent.
.jpg)
In the gear shaping process, a flat disc cutter is reciprocated over a fairly short stroke whilst rotated slowly
and being brought into contact with the counter-rotating workpiece.
The depth of contact is gradually increased over several revolutions of the workpiece, until the final depth of
cut has been achieved (not as diagram shows).
In both of these methods, a small range of cutter sizes is capable of producing a large variation in the number of teeth
on the finished gears.
This is achieved by adjusting the machines intermediate drive gears that link the rotation of the cutter to that
of the blank.
.jpg)
On completion of gearcutting, the depth of tooth cut is checked by placing a pair of suitably sized pins between opposite pairs of teeth and a measurement taken of the overall distance, comparing it against a set of special gear tables.
Click on the following link for more information on :
Where a gear, or other components requires teeth, splines, serrations or just a keyway in its bore, an alternative to gearcutting is to use the BROACHING process.
.jpg)
This involves the use of a very long, tapered shaft, having the required tooth-cutting profiles incrementally increasing along its length, with a roughing stage, a semi-finishing stage and the final finished stage.
In operation, the blank workpiece is mounted on the broaching machines bed and the small end of the broach is passed through its bore until it can be gripped by the jaws of pulling mechanism. The broach is then slowly pulled completely through the blank, the workpiece removed and the broach retracted to its start position, ready for the next component
The gearcutting department at AMC was located in the ground floor extension end of the factory and was equipped with a roughly equal number of shaping and hobbing machines, plus one large vertical broaching machine.
After setting up each machine to cut its own part, several of the machines could be supervised by one attendant, as the machining times would all be quite long, and different, allowing removing and re-loading of the components in a systematic order.
As well as the obvious gearbox components, other parts needing work in the gearcutters included timing gears and sprockets, primary drive sprockets, oil pump components and several pairs of parts using splined fits.
NOTE: For a time in the '60s, the AMC gearcutting department also sub-contracted work from Ford Cars, machining some of their helical gears, layshafts and speedo drive parts.
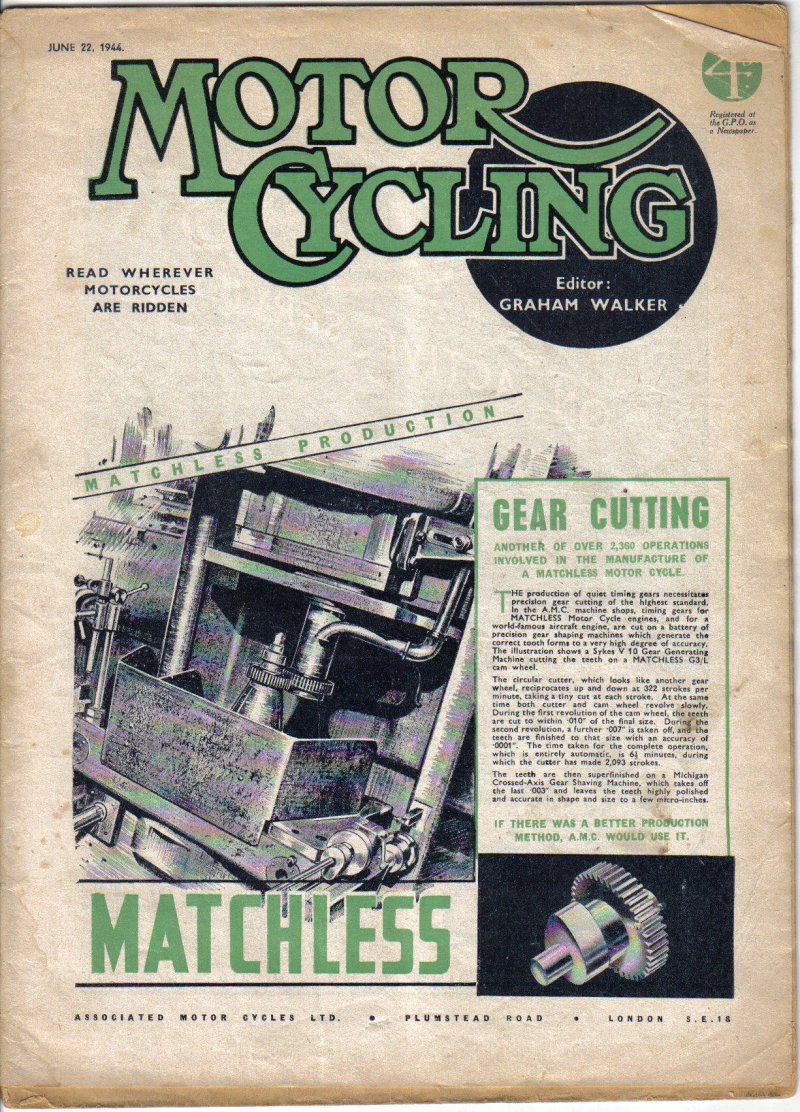
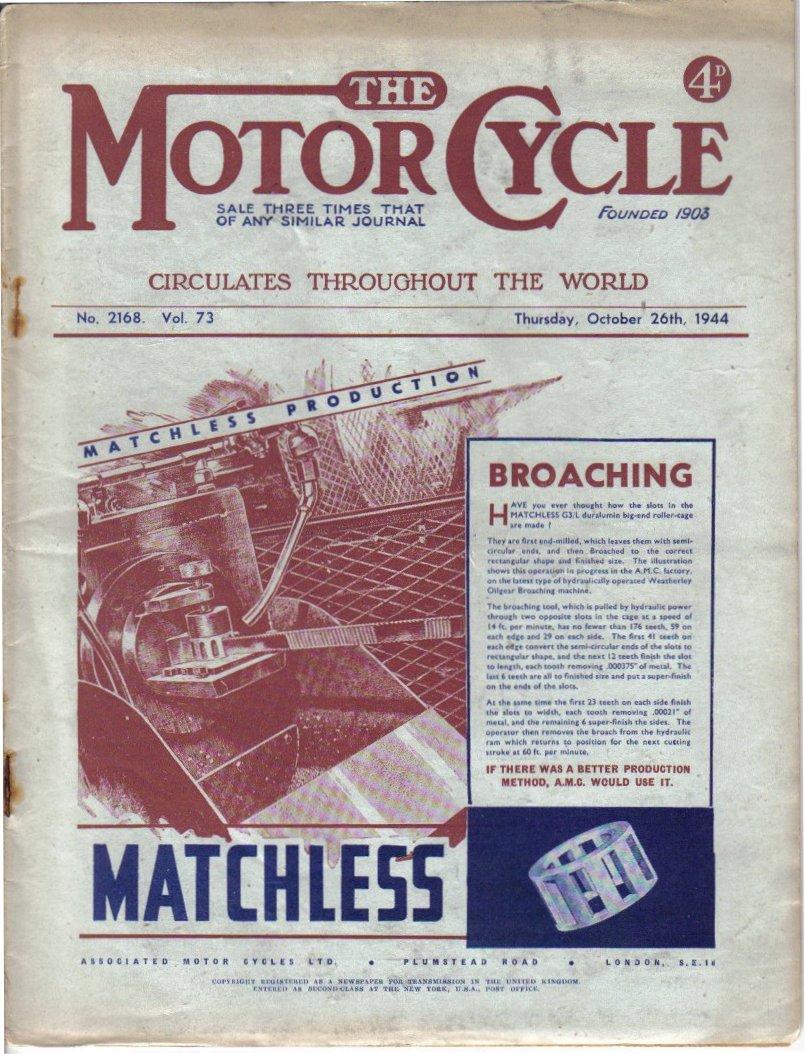
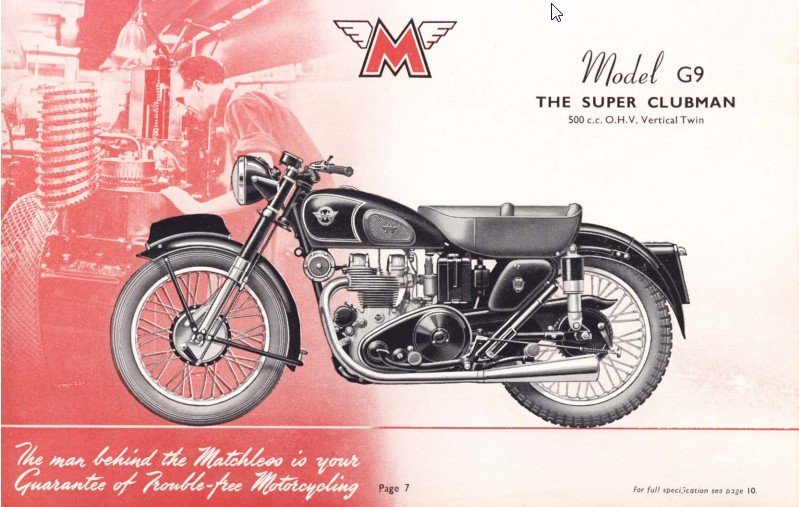
These Motor Cycle magazine cover pages and sales brochure feature work carried out in the gear cutting department.
(Click on the images to see enlarged views)
You can view the complete collection on Cover Pages.
Ron Bassett | ||
Ted Donovan | ||
Bill Eaglestone | 1956 (?) | |
Bert Gardiner | Foreman | |
Maurice Gibbons | ||
Harry Hatton | Hobbs | |
Ray Hazleton | ||
Charlie Horner | ||
Peter Sutton | 1956 - ? | Helical gears |
You can also view a group photo, taken on a coach outing in the early '50s, on the Scrapbook page.