Heat Treatment (Hardening)
.jpg)
Most of the components that make up a motor cycle (especially those in its engine and gearbox) are subjected to high operating speeds coupled with high stress levels.
Even when made of steel, these parts would have a life span measured in weeks rather than years, were it not for the selective application of heat treatment.
The term 'heat treatment' covers a wide range of different processes, but the overall aim is to alter the chemical constitution of the metal to provide the required levels of surface hardness (for wear), core strength (for stress handling) and ductility (for shock loading).
Associated Motor Cycles carried out all of its heat treatment in-house, so that it could have full control of the large range of processes needed for the end product.
The Heat Treatment Shop was located on the ground floor, at the Maxey Road end of the factory, and was fully equipped to carry out various methods of case hardening, direct hardening and other associated work.
Steel is a highly versatile metal whose properties, especially hardenablity, are linked to the exact proportions of
its two main constituents; iron and carbon.
This results in steel being grouped into three major classes: low-carbon (less than 0.2%), medium-carbon (between 0.2 and 0.5%) and high-carbon steel (higher than 0.5%).
Other sub-groupings of steels are those that have up to 8% of other alloying elements, such as manganese, nickel, cobalt, etc.(low-alloy steels) and any with a higher concentration, considered to be medium and high-alloy steels.
In the majority of motor cycle applications, the usual requirement would be for a hard contact surface to reduce wear
coupled with a relatively softer core to retain the ductility necessary for withstanding shock loads.
This combination is best achieved by using a low-carbon form of steel and infusing an extra carbon-rich layer into the
outer layer of the component by a process known as Carburising.
Subsequently, this outer layer is hardening by a process known as Case Hardening, in which the heated part is quenched
in water or oil, to trap the carbon in solution.
However, other parts, such as gearbox shafts, would have a need for a more rigid core to help resist the
bending stresses inposed on them. For these parts a medium-carbon steel (or more usually an alloy steel) would be best.
These materials would have sufficient carbon content to be Direct Hardened.
The following is a brief explanation as to how these processes were carried out at AMC, and the equipment used.
Case Hardening (carburising)
.jpg)
The simplest method involved packing the workpieces into rectangular cast iron pots, filled with granules of enriched charcoal.
Parts that had portions needing to stay unhardened (threads, etc.) would be covered with a soft fire clay coating,
or copper plated.
After sealing the lids with fire clay, the pots were placed into one of several 'open hearth' gas ovens at around 825°C, with the
resulting depth of case dependent on both the oven temperature and the length of time in the oven.
For obvious reasons, this was known as Pack Carburising.
Although a simple method of adding a carbon-rich layer to low-carbon steel components, it did not allow for the parts to be quenched after the pots were removed from the furnace. This meant that, after allowing the pots to cool down and be opened, the parts would have to be placed onto trays and then returned to the oven to be reheated, before they could be quenched in water
(You can read about John Rourks' first-hand experience of this process in his 'Memories of Plumstead' article on the Links page)
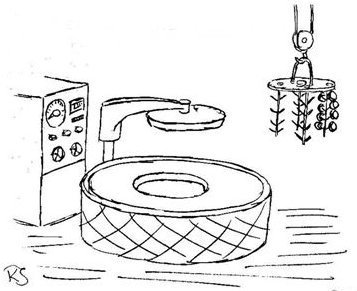
.jpg)
In gas carburising, the workpieces are held in a furnace containing an atmosphere of methane or propane which, at a temperature of around 925°C, causes carbon to diffuse into the surface before being quenched in oil to harden.
Another case hardening method was to string-up components on wires and suspend them in circular 'cauldrons' of molten sodium cyanide salts. This gave a thinner but harder case than pack carburising, but more care had to be taken due to the dangerous nature of the molten salts, which were prone to spit if any water were present on the steel parts.
Parts being carburised this way would need to be of a suitable shape for wiring up, or have tooling holes specially added.
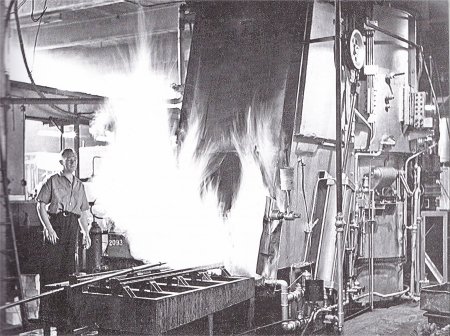
The carbo-nitriding furnace at AMC was the largest piece of heat treatment plant, situated in the centre of the department.
The process was similar to gas carburising with the addition of ammonia gas, which provides a source of nitrogen to give a harder case.
The interior of the furnace consisted of three sections: the loading area, the heating area above and the quenching tank below floor level.
A pair of rails allowed the movement in and out of a wheeled circular tub, filled with components to be treated, through an angled sliding door in the front of the furnace
Once inside, the tub would be automatically raised into the upper heating section, and the various gases introduced as required.
After the necessary diffusing time, the tub would automatically descend from the heating chamber, down past the loading area, into the quenching tank for hardening, before being raised again and withdrawn through the furnace door.
Whilst in operation, air would be kept out the furnace by lighting a controlled escape of gas around the sliding door (as the picture shows).
Direct Hardening
.jpg)
As mentioned earlier, direct hardening was the process that could be applied to steel parts that already had sufficient carbon content to be hardened by simply being heated and quenched.
The open-hearth gas furnaces were used for these heating operations with careful control needed of the temperature settings.
The main skill needed, though, was in the way that the quenching was carried out. With a long cylindrical item such as a gearbox shaft, each item would need to be lowered lengthwise into the quenching fluid (usually oil) in order to evenly cool it down. Otherwise a distorted shaft would result.
The use of alloy steels would help alleviate this distortion, by controlling the rate of cooling experienced throughout the thickness of the steel.
Induction Hardening/Annealing
Selective heat treatment was necessary on some parts that ruled out any of the usual methods.
Clutch push rods required only their extreme ends to be hardened, whilst any threads on the ends of hardened shafts needed to be annealed to reduce their brittleness.
Both these problems were overcome with the use of an Induction Hardening machine, that was initially located in the nearby Metallurgy Department, but subsequently moved into the Heat Treatment shop itself.
(See Metallurgy page for full description)
In 1962, the Dutch Motor magazine published a series of articles following a tour of the Plumstead Road factory.
You can read their brief observation of the Heat Treatment department in Part 4 of
'This is How Your AJS and Matchless is made'.
.jpg)
This Motor Cycle magazine cover page featured work carried out in the heat treatment department.
(Click on the image to see enlarged view)
You can view the complete collection on Cover Pages.
Harry Allcock | 1920-67 | Assistant Manager |
Charlie Damyon | Manager | |
Jack Godley | -1969 | Foreman |
John Rourke | (1921 - 61) | (dates incl. time in Drilling, Grinding, Inspection and other departments) |