Milling
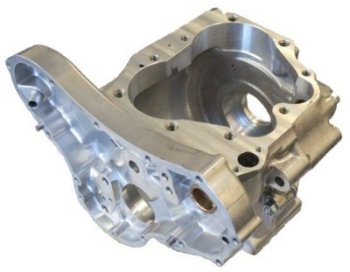
The machining of flat surfaces on motor cycle parts is almost always carried out on milling machines.
There are basically two type of milling machines: vertical and horizontal, and the work that can be carried out on each of them is quite specialised.
Both types had 3-axis movement, although the vertical height was normally only used for initial setting-up.
In the example of the crankcase shown here, the two main joint faces would have been machined on a vertical mill using a fly cutter, whilst the mounting lug faces, being semi-hidden, would need to be worked on a horizontal mill, with side and face cutters.
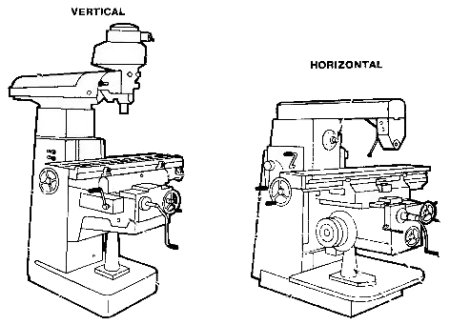
.jpg)
Vertical Milling
.jpg)
A very good example of the type of work that could be carried out on a vertical milling machine is the connecting rod of the AJS 7R racing engine.
.jpg)
Fracture of a connecting rod is one of the most common causes of catastrophic engine failure in racing motorcycles,
frequently putting the broken rod through the side of the crankcase and thereby rendering the engine irreparable.
So, to ensure the elimination of any forging imperfections that could act as stress raisers, as well as for weight-saving
purposes, every surface on this vital component was machined, using a variety of milling cutter types.
A small diameter bull-nosed cutter would have been used to machine the inside faces of the long rectangular recesses of the
central section of the rod, in order to achieve the important corner radius, also taking several traverses on the flat faces.
A larger diameter version would also be used to clean up the outer flange surfaces, using a rotary table to follow the path
around the big-end bore
For the round-bottomed lightening groove around the complete periphery of the con-rod, a convex-edged T-slot cutter would have been used with the con-rod again centred in various positions on a rotary table mounted on the milling machine worktable.
Horizontal Milling
.jpg)
An important feature of the horizontal milling machines used at AMC was the cutting tool arbor, which was a long circular bar fitted with several spacers and a sleeve bearing that allowed its outer end to be supported in a sturdy outrigger housing.
.jpg)
By this means, more than one cutter could be mounted onto the arbor, allowing the machining of multiple features simultaneously - a process known as gang-milling.
.jpg)
.jpg)
This swinging arm fork end casting is a good example of efficient machining of both inner and outer faces of the wheel spindle adjustment slot by gang-milling with two side and face cutters.
Here's just a few of the different cutter types used on both sorts of machines.
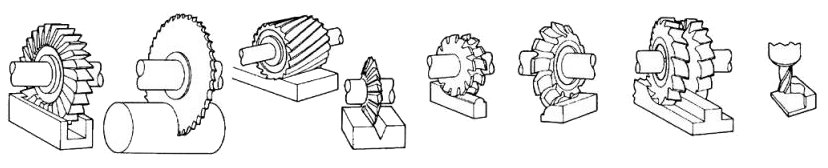
The milling department at AMC was situated on the ground floor, between the press shop and the gearcutters and was equipped with a large quantity of both types of mills, in separate groups.
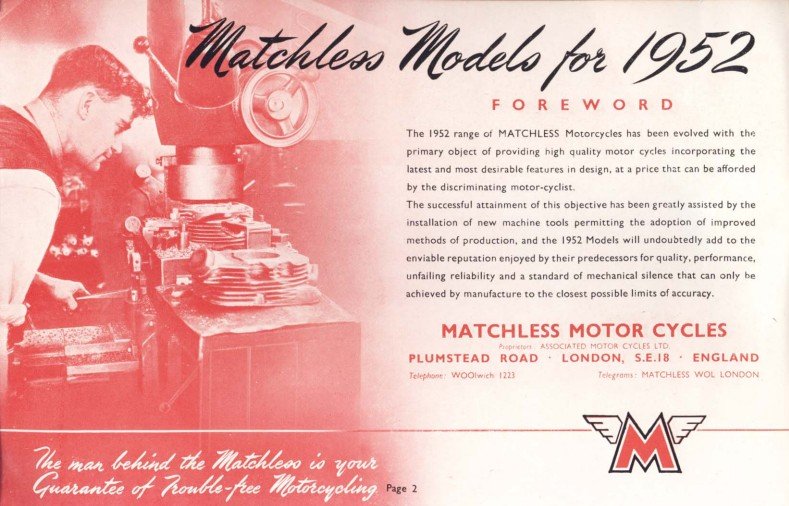
This sales brochure featured work carried out in the milling department.
(Click on the image to see enlarged view)
You can view the complete collection on Cover Pages.
You can also view a group photo, taken on a coach outing in the early '50s, on the Scrapbook page.
Ray Hazleton | ||
Bob Longhurst | ||
Bob Longhurst | ||
Peter McGue | ||
Ron Smith | ||
Peter Stevens | ||
Leslie Vickary | Setter | |
Stan Ward | Foreman | |
Harry Whitehead |