Finishing
.jpg)
The engineering of AJS and Matchless machines was always regarded as second to none in the motorcycle world, and the quality of the finish of the bikes matched this excellence.
The finishing processes at AMC could conveniently be called the three-Ps; Painting, Plating and Polishing, with Preparation being an important pre-requisite to each of them.
All of the finishing work was carried out on the first floor, taking up almost the total floor area of the original, pre-extended factory.
However, the preparation processes involved the use of hazardous chemicals and were therefore done separately.
All items to be painted were first given a phosphate coat (Bonderised) as a bonding agent and to prevent rust and this was done in one of the Roof Shops.
Rough aluminium castings that were not to be subsequently polished were cleaned by dipping in an acid bath which was located in the basement under the Packing Department.
Painting
.jpg)
Painting (or more precisely stove enamelling) was the finish used on the majority of cycle parts; frames, petrol and oil tanks, toolboxes and most other sheet metal components.
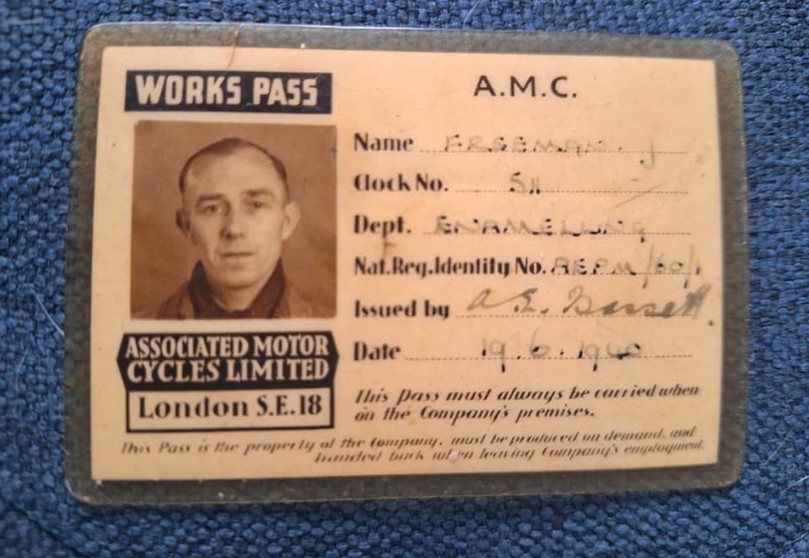
Welded frames were the only items that were sprayed by conventional methods. For AMC brazed frames and most of the other parts, the process involved either dipping the items in a bath of paint or pouring the paint over them from a ladle.
After whatever method of paint application, the parts were then hung up on a conveyor system that took them slowly through an oven, to 'stove' or cook the paint.
The usual practice was to repeat this process up to three times in most cases, to produce a final finish that would withstand the rigours of whatever the roads and climate could throw at it.
In 1962, the Dutch Motor magazine published a series of articles following a tour of the Plumstead Road factory.
You can read their brief observation of the Painting department in Part 4 of
'This is How Your AJS and Matchless is made'.
Plating
.jpg)
The plating shop was the place where plain, grey, nondescript metal parts were transformed into gleaming, mirror-finish items that made a bike look much more than just an everyday means of transport.
However, the process itself was carried out in quite grim conditions and dealt with what could be dangerous chemicals, back in the days when health and safety considerations were not quite what they are today.
There are two principal classes of chromium plating; decorative, in which thin coatings serve as a non-tarnishing, durable surface finish and industrial or 'hard' chromium, where heavy coatings are used to take advantage of the special properties of chromium, which include resistance to heat, wear, corrosion, erosion, low coefficient of friction and anti-galling.
Decorative chrome is almost always plated on top of a nickel or copper/nickel layer, which seals off the substrate so that the micro-cracking chrome deposit does not present corrosion problems.
This was the process used at AMC for the vast majority of visible components, although the alternative 'hard' version was also used on some cam follower faces and as a means of reclaiming worn parts, such as the many plug gauges used in the factory workshops.
.jpg)
Other steel parts that didn't need such a highly decorative finish, but still required corrosion preventive treatment, would have been cadmium plated. This was a sacrificial coating (like zinc) that would carry on protecting the underlying metal even when damaged itself.
Cadmium plating also acted as an effective barrier to prevent the galvanic/bimetallic reaction between steel and aluminium parts, whilst its low coefficient of friction reduced the tightening torque on threaded components, and allowed repetitive dismantling.
.jpg)
AMC used cadmium plating on all of its fastenings (nuts, bolts, screws, washers) and several other components, such as wheel spindles.
Due to the quantity needing processing, and their relatively small sizes, fasteners had the cadmium applied mechanically, by 'tumbling' them in a rotating barrel filled with a mixture of glass beads, proprietary chemicals, water and metal powder.
It had it's drawbacks, though, as high-tensile steel parts could suffer breakage due to hydrogen embrittlement, requiring a subsequent passivation treatment to correct the problem.
Although superior in many ways to other protective coatings, it was later deemed to be a hazardous process when the toxic effects of cadmium became apparent.
Industrial limits on cadmium exposure were reduced in most industrialized nations after the 1960s.
Polishing
.jpg)
For the obvious reason of lightness, a great many of a motorcycle's parts are made of aluminium, larger ones in the form of castings.
For the relatively low production runs required, and also for its adaptability, the sand casting method was used predominantly by the foundries that AMC contracted their work to.
In their natural state, however, the resulting cast aluminium parts are relatively rough, with a flat silver finish that, whilst acceptable on semi-hidden parts, needs a degree of enhancement by polishing on the more visible ones, such as engine timing and primary drive covers and brake plates.
A description of the polishing shop in the late '40s describes it as being "pitch black, with rows of big electric motors running the grinding and felt wheels. A rough casting had to be cleaned up with a coarse emery wheel before polishing, and that produced a lot of metal dust.
Each polisher had a naked light bulb over each wheel and a crude dust extractor that exhausted on the roof to pollute the neighbourhood. The younger men would wear a dust mask, but the older workers just inhaled the stuff and would spit occasionally to get rid of the grit"
Brian Slark 'Working for AMC' - Classic Bike magazine July 1988
It's worth bearing in mind that none of the three methods of finishing employed at AMC would be able to cover up defects in a part, so this preparation was essential. Enamelling and chrome plating had an uncanny way of emphasising any brazing spatters, dents or specks of grit on a surface.
Working in a firm that had its own finishing departments was a bonus point to many of the staff, as there was always the opportunity to keep your own private motorcycle parts in top condition, by slipping them into the hands of the relevant person for a 'lunch time' job.
The usual trading currency for this work being a half-ounce of Golden Virginia tobacco or its nearest equivalent!!
.jpg)
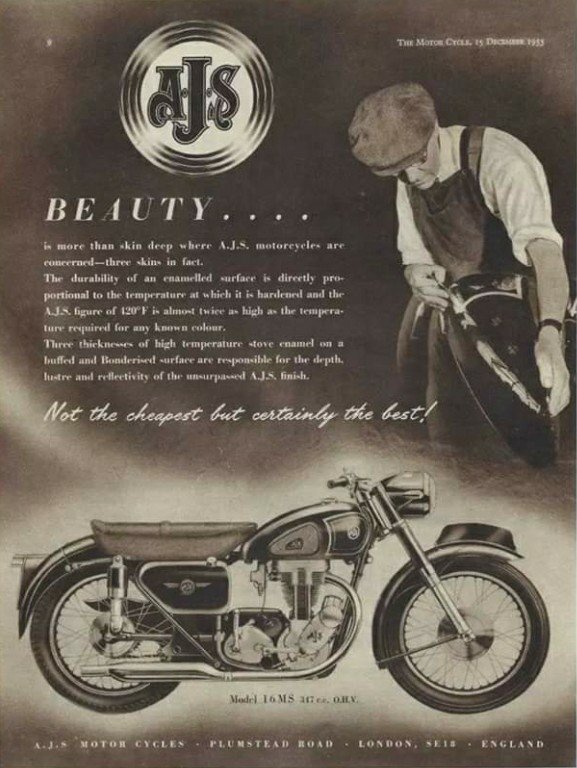
.jpg)
This Motor Cycle magazine cover page and posters featured work carried out in the finishing department.
(Click on the image to see enlarged view)
You can view the complete collection on Cover Pages.
Bill Freeman | Enamellers - tank lining | |
George Higgs | Enamellers | |
Charlie Day | Enamellers - foreman | |
Fred Grimmer | Plating Shop | |
Harold (Harry) Grimmer | 1946-1969 | Plating/Polishing Shop |
Alan Fisher | Plating Shop | |
Chris Fisher | Plating Shop | |
Ernie Thomas | Polishers | |
Nobby Baker | Polishers | |
Tony Barbett | Polishers | |
Nobby Clarke | Polishers | |
Les Francis | Polishers | |
Georgie Gardener | Polishers | |
Jack Hall | Polishers | |
Charlie Hood | Polishers | |
? Hutchings | Polishers | |
Charlie Wood | Polishers |