Inspection
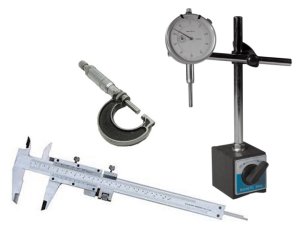
The inspection department (or view room as it was also called) was a glass panelled area situated on the ground floor, close to the factory entrance (later moved to make space for the semi-auto machines), and was responsible for checking samples from each batch of components of manufactured components.
To carry out this work, the department was well equipped with a wide range of specialist tools, including a shadowgraph (for viewing enlarged profiles of features like gear teeth), pneumatic bore gauges (for checking the size of cylinder bores), hardness and crack testing facilities and a whole multitude of plug and gap gauges as well as internal and external micrometers.
For those unfamiliar with some of these devices, here are a few descriptions:
Pneumatic gauges
.jpg)
The pneumatic (or air) internal gauges were devices that allowed the machining of cylinder bores to be more accurately measured than could be achieved by any, more usual, mechanical means.
The equipment comprised a hand held probe, much like a standard plug gauge, which had various small holes around its circumference through which a controlled level of pressurized air was allowed to escape.
The rate of air escape was measured by a meter which then translated it to a diametral measurement; the more air escaping corresponding to a larger bore, and vice versa.
Shadowgraph
.jpg)
The Shadowgraph (sometimes known as a comparator or profile projector) was an optical device that allowed the profiles of parts to be examined and measured, under various degrees of magnification, as silhouettes on a viewing screen.
The accuracy of the process was dependent on the use of various lenses, the most important being the collimator through which the light rays from the illumination source were made to emerge in a parallel formation.
The object to be examined was mounted on an adjustable platform, positioned between the collimator and enlargement lens, and its resulting magnified image thrown onto the machine's screen where accurate measurements could be made by various techniques.
As well as allowing the checking of thread pitches and flank angles, the shadowgraph was an invaluable tool for confirming the machined profiles of gear teeth and cams. This was achieved by placing a scaled-up tracing of the required shape onto the screen which could then be compared with the actual part's silhouette, any differences being quite apparent.
Hardness Tester
.jpg)
Although the heat treatment shop was equipped with its own testing machine, it was one of the functions of the inspection department to carry out routine tests on samples of all hardened parts on its own equipment.
.jpg)
In operation, the part to be be inspected was first polished over a small area and place on the adjustable carriage of the tester.
Weights would be selected (depending on the expected level of hardness and, if case hardened, the depth of case) and placed on a carrier suspended from the loading arm of the machine.
The sample part would then be positioned with its polished face close underneath the diamond indenter of the machine and the automatic loading cycle initiated by operating a foot pedal.
.jpg)
Once the indenter had been retracted, the specimen would be moved across the machine to view the resultant indentation under a microscopic attachment which included a built-in measuring device (ocular counter) featuring individually adjustable knife edges that could be set to just touch each side of the indentation.
.jpg)
A Vickers hardness tester was normally used as it utilised a pyramid-shaped diamond indenter, rather than the Brinell circular shape.
The resultant square image was easier to obtain accurate readings from, by aligning two adjustable blades with the diagonal corners of the impression.
The ocular counter reading (the Vickers Pyramid numeral or VPN) could then be read off and, with the use of tables, converted into the hardness value (HV) for the material.
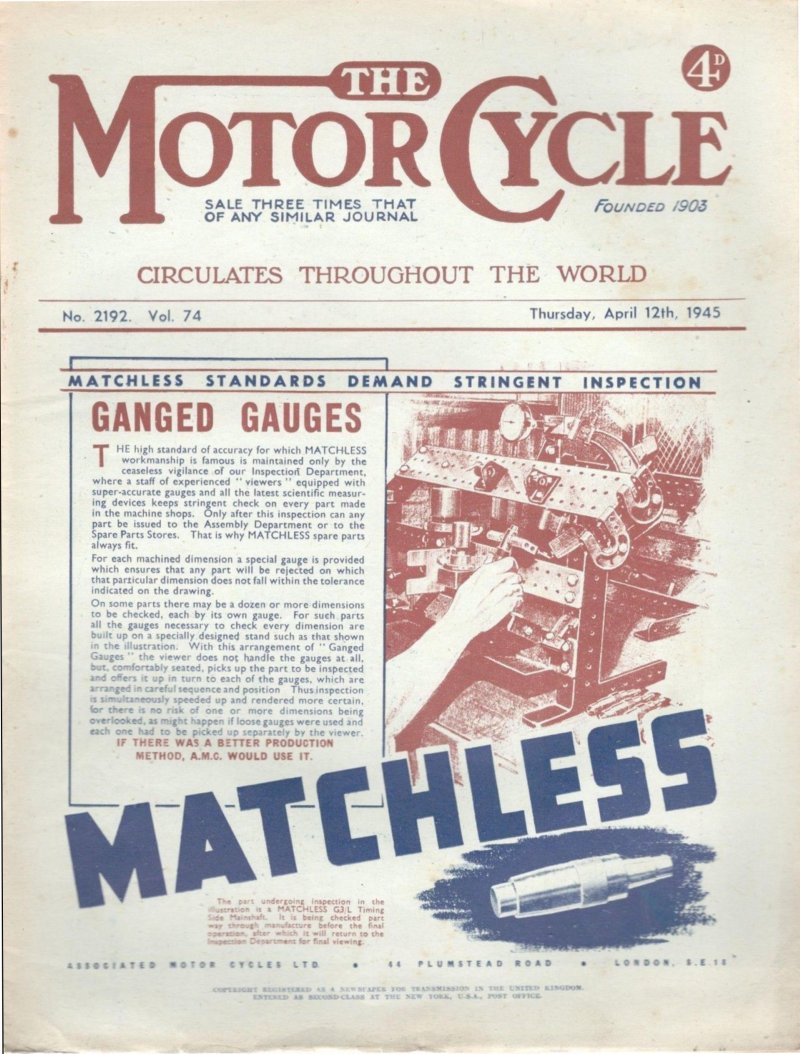
.jpg)
.jpg)
These Motor Cycle magazine cover pages and poster feature work carried out in the inspection department.
(Click on the images to see enlarged views)
You can view the complete collection on Cover Pages.
Charlie Amdo | ||
Charlie Arnold | ||
Frank Bugs/Boggs | ||
Harry Briley | 1915 - 48+ | |
Robert A Hancock | 1940 - 46 | |
Bill Horton | Foreman | |
Joan Jolly | ||
Harry Larner | ||
Alfred Lipscombe | Later in Accounts | |
John Rourke | (1928 - 61) | (dates incl. time in Drilling, Grinding, Heat Treatment and other departments) |
Rose Rourke | 1944 - 62 | |
Peter Stevens | ||
Charles Timberlake | (Colliers) |